La refrigeración industrial y comercial enfrentan actualmente uno de sus mayores desafíos: las fugas de gas refrigerante. Estas fugas no solo representan un problema operativo, sino que también tienen un impacto significativo en el medio ambiente y en los costos asociados al mantenimiento y operación de los sistemas de refrigeración.
En este artículo, exploraremos las causas y consecuencias de las fugas de gas refrigerante, así como las medidas necesarias para minimizarlas y cumplir con las normativas internacionales vigentes.
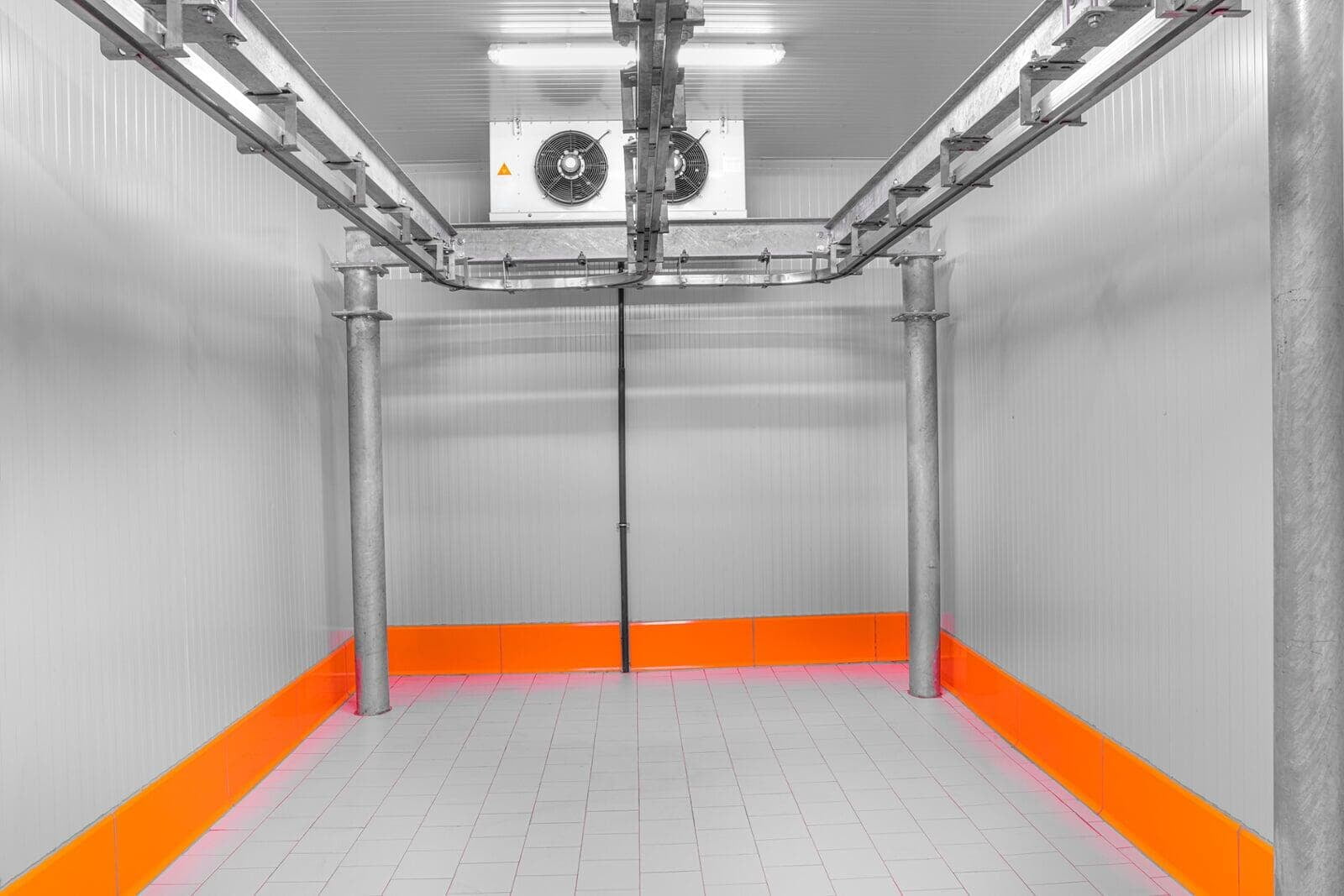
Impacto ambiental y normativas internacionales
Impacto ambiental y normativas internacionales
En las últimas décadas, la creciente preocupación por el calentamiento global ha impulsado a las naciones a adoptar medidas como los Protocolos de Montreal (1988) y Kioto (1992), que buscan reducir el uso de refrigerantes que afectan la capa de ozono y contribuyen al cambio climático. Estos esfuerzos han llevado a la eliminación progresiva de refrigerantes como los CFC y HCFC, que son altamente perjudiciales para el medio ambiente.
El Acuerdo de Kigali, firmado en diciembre de 2016, marcó un hito al establecer que 197 países se comprometen a reducir gradualmente los refrigerantes HFC. Estos refrigerantes, aunque menos dañinos que sus predecesores, siguen teniendo un elevado Potencial de Calentamiento Global (PCA), lo que resalta la importancia de evitar su liberación a la atmósfera.
La importancia de la prevención de fugas
La importancia de la prevención de fugas
La pérdida de refrigerante reduce la eficiencia del sistema de refrigeración, lo que a su vez aumenta el consumo energético. Además, es esencial integrar nuevas herramientas, técnicas, procedimientos y sistemas de detección y gestión que minimicen las fugas de gases refrigerantes.
Esto es especialmente relevante en la refrigeración comercial, donde las tasas de fuga pueden variar entre el 15% y el 33% anual, según datos de la Agencia de Medio Ambiente y Control de la Energía de Francia (ADEME).
Características y vulnerabilidades de los sistemas de refrigeración
Características y vulnerabilidades de los sistemas de refrigeración
Las instalaciones frigoríficas que operan con el ciclo de compresión de vapor requieren un fluido refrigerante que circula a través del sistema, cambiando de estado de vapor a líquido en el condensador y de líquido a vapor en el evaporador. Este proceso debe cumplir con ciertas condiciones:
- Estado gaseoso: los refrigerantes deben estar en estado gaseoso a las presiones y temperaturas ambientales habituales.
- Presión elevada: dentro del sistema frigorífico, el refrigerante generalmente se encuentra a una presión mayor que la atmosférica.
Estas condiciones hacen que cualquier falla en la estanqueidad del sistema, por mínima que sea, pueda resultar en una fuga y mantener la estanqueidad total a lo largo de la vida útil del sistema es complicado debido a factores como variaciones de presión, temperatura, vibraciones y mantenimiento.
Causas principales de la degradación de estanqueidad
Causas principales de la degradación de estanqueidad
Estudios recientes, como los contenidos en la ADEME (Agencia de Medio Ambiente y Control de la Energía de Francia), han identificado nueve causas principales que contribuyen a la degradación de la estanqueidad en sistemas frigoríficos:
- Soldaduras defectuosas: errores en las uniones soldadas pueden crear puntos débiles propensos a fugas.
- Ajustes inadecuados de tuercas y tornillos: tanto los ajustes insuficientes como los excesivos pueden afectar la estanqueidad, permitiendo la fuga de refrigerante.
- Tapones de válvulas no colocados: la omisión de estos elementos esenciales facilita la pérdida de gas.
- Incompatibilidad de componentes con aceites de lubricación (retrofit): el uso de componentes que no son compatibles con los aceites de lubricación puede provocar deterioro en las juntas y sellos, facilitando las fugas.
- Vibración excesiva de componentes mecánicos, especialmente compresores: las vibraciones continuas pueden aflojar conexiones y generar pequeñas fisuras.
- Expansiones térmicas: los cambios de temperatura causan expansión y contracción de los materiales, lo que puede generar fisuras en las uniones.
- Corrosión provocada por alimentos: en instalaciones comerciales como muebles refrigerados, la corrosión inducida por el contacto con alimentos puede comprometer la integridad del sistema.
- Contacto entre metales (cobre-hierro): este tipo de contacto puede llevar a la abrasión o corrosión galvánica, creando puntos vulnerables.
- Soporte inadecuado de tuberías: la falta de soporte adecuado puede generar tensiones adicionales en las uniones, incrementando el riesgo de fugas.
La identificación y mitigación de estas causas son esenciales para prolongar la vida útil de los sistemas frigoríficos y minimizar el impacto de las fugas de refrigerante.
¿Qué es el sobrecalentamiento y por qué es importante?
¿Qué es el sobrecalentamiento y por qué es importante?
El sobrecalentamiento se refiere al aumento de temperatura del refrigerante en estado de vapor después de haber absorbido suficiente calor para evaporarse completamente. Este proceso asegura que el refrigerante que llega al compresor esté en fase de vapor, lo que es fundamental para evitar que el compresor sufra daños por la entrada de líquido refrigerante, pues la presencia de líquido puede causar daños mecánicos severos.
También sirve como un indicador del estado de la carga de refrigerante en el sistema. Un bajo nivel de sobrecalentamiento puede indicar un exceso de refrigerante en el sistema, mientras que un sobrecalentamiento alto puede sugerir una carga insuficiente.
El sobrecalentamiento refleja cuán eficientemente está funcionando el evaporador. Si el serpentín del evaporador está bien lleno de refrigerante en ebullición, puede absorber más calor del ambiente o del objeto que se desea enfriar. Sin embargo, si hay demasiado refrigerante en el evaporador, existe el riesgo de que no se evapore por completo, lo que puede llevar a problemas de rendimiento y daños en el compresor.
Mantener un sobrecalentamiento dentro del rango óptimo (generalmente entre 20°F y 30°F para la mayoría de los compresores) asegura que el sistema de refrigeración opere de manera estable y confiable. Esto evita fluctuaciones que podrían afectar el rendimiento del sistema y la calidad del enfriamiento.
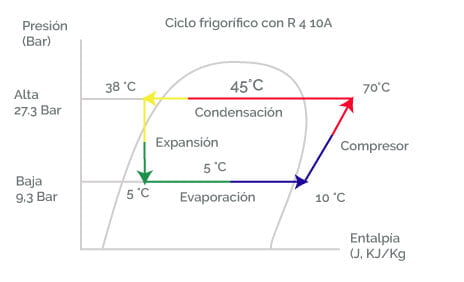
Cuando un sistema de refrigeración opera con menos del 100% de la carga mínima requerida de refrigerante, su eficiencia disminuye, lo que lleva a un aumento en el consumo de energía. Por ejemplo, un sistema que funciona con solo el 80% de la carga mínima de refrigerante puede llegar a consumir un 15% más de energía en comparación con un sistema que opera con la carga adecuada. Este incremento en el consumo energético se traduce directamente en mayores costos de operación.
La relación entre el porcentaje de fugas de refrigerante y el costo de funcionamiento de la instalación se puede visualizar claramente:
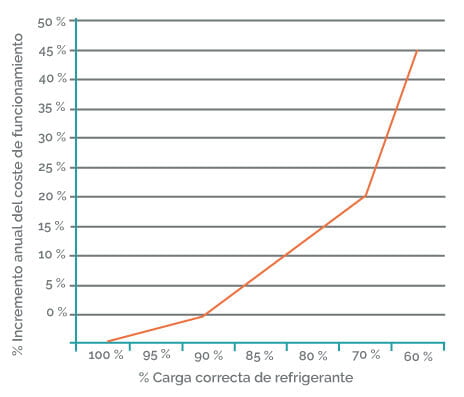
Consecuencias de las fugas en sistemas de refrigeración
Consecuencias de las fugas en sistemas de refrigeración
- Operativas. Una fuga reduce la eficiencia de enfriamiento del sistema, lo que aumenta la operación del compresor y disminuye el confort en las instalaciones. Esto genera un aumento en el intercambio de calor en los evaporadores y disminuye el sobrecalentamiento del sistema.
- Económicas. Las fugas incrementan el consumo energético del sistema, elevando los costos operativos. Por ejemplo, un sistema de refrigeración que opera con solo el 80% de la carga mínima de refrigerante requerida puede consumir hasta un 15% más de energía. Además, se generan otros costos asociados, como la reposición del refrigerante, la reparación de la fuga y la pérdida de mercancías por fallos en la cadena de frío.
- Medioambientales. Los refrigerantes HFC, al ser liberados a la atmósfera, tienen un efecto invernadero mucho mayor que el CO₂. Por ejemplo, liberar 1 kg de R404A equivale a emitir 3800 kg de CO₂. Además, la generación de electricidad adicional necesaria para compensar la pérdida de eficiencia también produce emisiones de CO₂, agravando el impacto ambiental.
El Total Equivalent Warming Impact (TEWI) es una medida que combina los efectos directos e indirectos de un sistema de refrigeración sobre el calentamiento global y las fugas de refrigerante aumentan el TEWI, lo que resalta la importancia de prevenirlas.
- Seguridad. Esto incluye riesgos como la liberación de refrigerante en áreas mal ventiladas, efectos narcóticos, problemas cardíacos, toxicidad del vapor y daños corrosivos en ojos y piel.
Los refrigerantes de bajo Potencial de Calentamiento Global (GWP) generalmente tienen una baja estabilidad atmosférica, lo que significa que se descomponen más rápidamente en la atmósfera. Esta característica es beneficiosa para reducir el calentamiento global, pero también introduce riesgos de inflamabilidad, ya que muchos de estos refrigerantes pertenecen a las categorías A2L, A2 y A3, según la clasificación de inflamabilidad.
Estos grupos están definidos de la siguiente manera:
A2L: refrigerantes ligeramente inflamables.
A2: refrigerantes moderadamente inflamables.
A3: refrigerantes altamente inflamables.

Para mitigar estos riesgos, es fundamental seguir normativas y guías establecidas por organismos como ASHRAE 34-2022 y ASHRAE 15-2022 que proporcionan directrices claras sobre la clasificación de refrigerantes y los requisitos de seguridad necesarios para las instalaciones que utilizan refrigerantes inflamables.
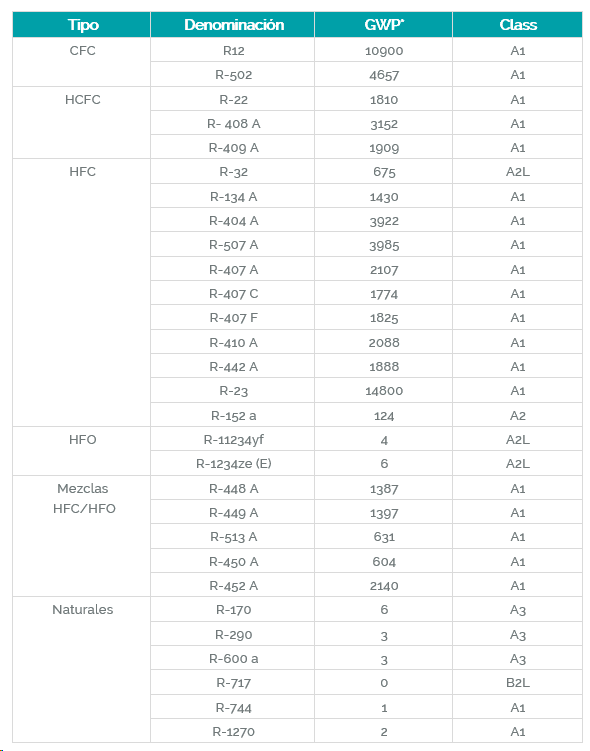
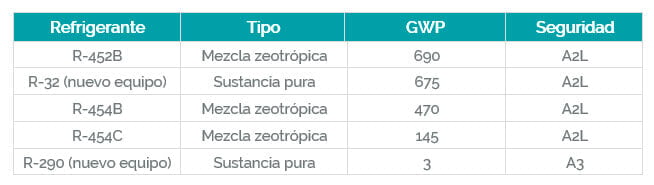
Clasificación de refrigerantes
Clasificación de refrigerantes
Las letras minúsculas en los refrigerantes, como en el caso del R-134a, indican un gas isómero. Esta letra señala la simetría en los pesos atómicos del compuesto. El refrigerante más simétrico no lleva letra, mientras que aquellos con mayor asimetría se identifican con letras como a, b, c, etc.
Por otro lado, las letras mayúsculas se utilizan para denotar mezclas zeotrópicas. Estas mezclas pertenecen a la serie 400. Las letras A, B, C, etc., que siguen al número en la designación del refrigerante, permiten distinguir entre mezclas que contienen los mismos componentes, pero en diferentes proporciones. Ejemplos de refrigerantes zeotrópicos incluyen el R-401A, el R-422B y el R-407C.
En resumen, las mezclas azeotrópicas, clasificadas en la serie 500, son fundamentales en la refrigeración debido a su comportamiento homogéneo, que garantiza la misma composición tanto en la fase líquida como en la de vapor. Ejemplos de estos refrigerantes, como el R-502 y el R-507, destacan por su fiabilidad y eficiencia en aplicaciones críticas.
En KINENERGY, comprendemos la relevancia de estos componentes y los rigurosos procedimientos asociados para garantizar un rendimiento óptimo y seguro de los sistemas de refrigeración.
Nuestro equipo está capacitado para ofrecer asesoramiento y servicios de alta calidad en el diseño y verificación de estos sistemas. Si deseas obtener más información o necesitas asistencia especializada, no dudes en dejarnos tus datos.
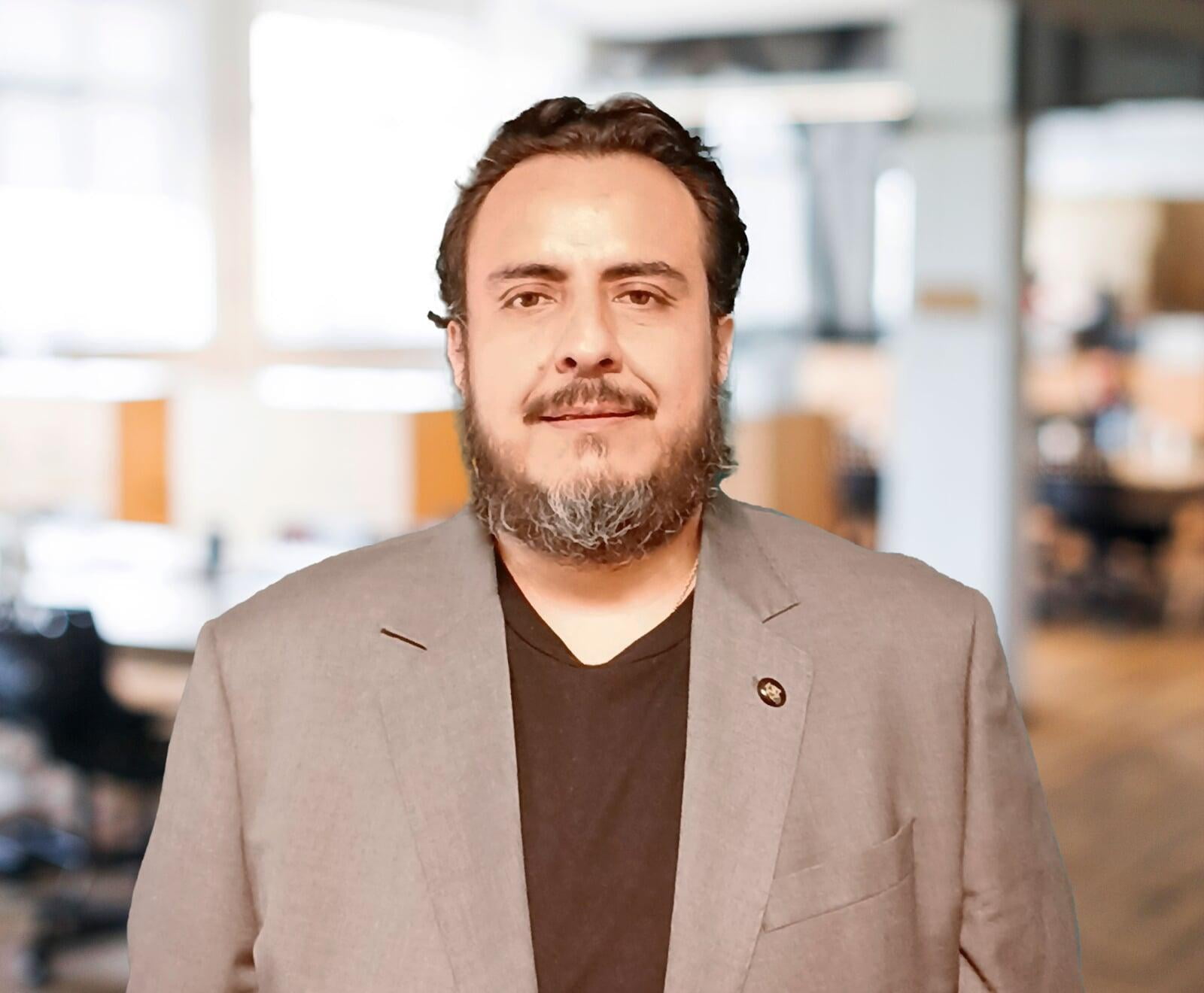
José Luis Arcos
Coordinador HVAC
Coordinador HVAC
Cuenta con más de 14 años de experiencia en sistemas de HVAC (Heating, Ventilation, Air Conditioning), ha desarrollado actividades en el área de diseño, instalación y TAB (Testing, Adjusting and Balance) de sistemas de climatización en bancos, centros de telecomunicaciones, retail, hoteles, centros comerciales y edificios.
En 2016 se unió a KINENERGY como especialista en comisionamiento en HVAC, donde se ha enfocado en el desarrollo de pruebas funcionales a sistemas de HVAC para certificación LEED hasta la realización de pruebas integrativas de commissioning nivel 5, de igual manera ha participado en diversos proyectos realizando pruebas de Cx, TAB, pruebas a envolvente y de integrity room, en México, Centroamérica y Sudamérica.
Cuenta con más de 14 años de experiencia en sistemas de HVAC (Heating, Ventilation, Air Conditioning), ha desarrollado actividades en el área de diseño, instalación y TAB (Testing, Adjusting and Balance) de sistemas de climatización en bancos, centros de telecomunicaciones, retail, hoteles, centros comerciales y edificios.
En 2016 se unió a KINENERGY como especialista en comisionamiento en HVAC, donde se ha enfocado en el desarrollo de pruebas funcionales a sistemas de HVAC para certificación LEED hasta la realización de pruebas integrativas de commissioning nivel 5, de igual manera ha participado en diversos proyectos realizando pruebas de Cx, TAB, pruebas a envolvente y de integrity room, en México, Centroamérica y Sudamérica.
Referencias:
ASHRAE 34-2022 y ASHRAE 15-2022 para normativas de seguridad en refrigerantes.
Acuerdo de Kigali, 2016: reducción gradual de HFC.
Refrigerant Loss, System Efficiency and Reliability – A Global Perspective; GEA Refrigeration UK Ltd for Institute Of Refrigeration (IOR). ©Institute of Refrigeration Annual Conference 2013.