Como lo comentamos en la primera parte del artículo, el reporte del TAB proporciona un valioso registro en papel de todos los cambios realizados en tus sistemas de HVAC, esta información genera tanto para el diseñador como para el cliente final grandes beneficios al ayudar a tomar mejores decisiones y enfocarse en invertir en lo principal que es el negocio, en lugar de solucionar problemas que bien pudieron haberse resuelto si se hubiera realizado el TAB en tiempo y forma.
Como caso práctico de la industria alimenticia compartimos uno de tantos problemas que existían dentro de las líneas de producción.
Los más significativos eran 3:
- Contaminación del producto por polvos saborizantes.
La presión diferencial a la cual se estaban manejando algunos espacios disentía de la requerida por el diseño, ya que algunas materias primas utilizadas como saborizante del producto volaban a través de las líneas de producción y contaminaban otros productos, o áreas que requerían estar en presión negativa estaban presurizadas y viceversa.
- Rechazo de lotes de producto terminado debido a que no cumplía con el perfil organoléptico (aspecto aroma, sabor, textura y color) y/o los requerimientos específicos del producto (Peso, Ph, humedad y dimensiones).
Debido a que la humedad relativa en el espacio de producción era más alta que la requerida, provocaba que el producto final adquiriera mayor humedad del ambiente. Esto a su vez, da como resultado que este no cumpliera con los estándares de calidad y por lo tanto aumentó el desperdicio de la producción.
- La calidad en el producto terminado no era constante y dependía de factores externos (clima, humedad ambiental y temperatura).
Lo anterior, debido a que la operación del sistema de automatización era deficiente por lo cual no había un control de la operación de los equipos. Esto repercutía en problemas tales como:
- Mayor cantidad de enfriamiento en algunos espacios que no requerían enfriamiento, mientras que en los espacios donde había condiciones específicas de temperatura y humedad estas no podían ser controladas.
- La comunicación de los equipos era intermitente por lo que no se podían obtener las gráficas de comportamiento certeras y requeridas de acuerdo con las necesidades del espacio.
- La falta de expertise para la operación del sistema provocaba intermitencias en el servicio, lo cual no ayudaba ni al personal de mantenimiento, ni al personal de producción a determinar cuál era la causa raíz del problema.
El punto que estudiaremos dentro de este caso práctico será la contaminación cruzada.
Análisis de la capacidad de los equipos actuales
Para determinar si los equipos que se encontraban en operación contaban con las capacidades para mantener los parámetros de presurización deseados, se analizó la información recopilada y se contrastó con la información de diseño. Los criterios que fueron tomados para determinar si se requerían equipos adicionales son los siguientes:
- El sistema de HVAC se encontró operando de acuerdo con diseño.
- Las infiltraciones entre los espacios son por las aperturas que existen entre un espacio a otro, por continuidad de la línea de producción.
- Las puertas rápidas se encontraban cerradas la mayoría del tiempo.
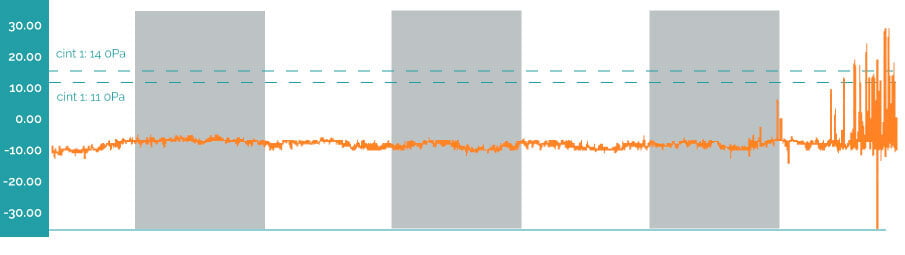
En los diferentes espacios de producción se requerían ciertos niveles de presurización, ya que estos permitían que no hubiera contaminación cruzada entre un espacio de proceso y producto. Dichas condiciones no eran alcanzadas con los equipos instalados, ya que la presión de los cuartos se encontraba por debajo de lo deseado, debido a que las secuencias de operación no estaban siendo ejecutadas de manera adecuada, además de contar con infiltraciones que no fueron consideradas durante diseño.
Las opciones planteadas para el control de los problemas de flujos de aire entre espacios y por consecuencia contaminación de una zona a otra fueron de tres tipos:
- Colocación de barreras físicas y sellado de infiltraciones.
- Barreras no físicas; cortinas de aire.
- Ajuste de flujos de inyección y extracción de aire en las cantidades requeridas para mantener los parámetros requeridos de presurización entre espacios.
Implementación 1: Ajuste de flujos de aire de entrada y salida
Ajuste de todos los valores de extracciones e inyección de aire exterior, para que estos funcionen con flujos constantes. Para realizar dicho arreglo se requiere previamente que el sistema de automatización este 100% funcional y que se tenga la capacidad de ajustar a través del sistema la apertura y cierre de las compuertas, así como fijar los parámetros mínimos de flujo de aire exterior dentro de la secuencia de operación.
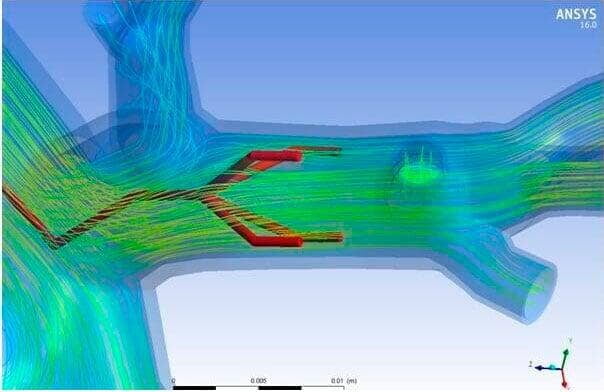
Implementación 2: Ajuste de flujos de aire de entrada y salida modulante con BMS
En caso de que se requiera que los flujos de extracción e inyección de aire no permanezcan constantes, sino que estos modulen de acuerdo con la presión requerida, se deberá implementar un sistema de BMS que realice un control integrado entre las RTU y extractores dentro de una misma zona, así como una medición de presión de zona, implementando una secuencia de operación que permita fluctuar los volúmenes de aire dependiendo de las necesidades del espacio.
Implementación 3: Instalación de cortinas de aire o cierre de puertas
Con base en las mediciones de diferencial de presión que se obtuvieron, una de las recomendaciones realizadas fue considerar la instalación de cortinas de aire para reducir la infiltración de aire de un espacio a otro o el cierre de estas aperturas.
Estas recomendaciones fueron con base en la tabla de presiones diferencias medidas con los equipos entre espacios.
Implementación 4: Incremento de capacidades de ventilación y enfriamiento
De acuerdo con las capacidades actuales y los requerimientos de presurización, algunos espacios requerían volumen de aire adicional y para no afectar las condiciones de diseño se tenía que adicionar capacidad de enfriamiento. Esto repercutía en un sistema más robusto, y una mayor inversión.
Conclusiones
El cliente final adopto por ajustar su sistema de aire a través del BMS, ya que contaba con la infraestructura requerida, por lo que fue la opción que tenía que realizar menor inversión de capital.
Si se hubiera realizado el proceso de TAB una vez terminada la planta y con los equipos de producción operando, se hubieran evitado tener tantos problemas de producción como los que se encontraron, ya que se hubieran detectado a tiempo y se hubiesen podido corregir previo al inicio de la producción, ya que se hubiera contado con un reporte de que estaba pasando y cuáles eran las posibles soluciones.
Haberlo realizado con la operación al 100% de la planta de producción implico un reto para nuestro equipo ya que la cantidad de horas de espera para no afectar la producción y los tiempos muertos nos dejaba tiempos de permanencia de más de 12 horas dentro de las instalaciones.
Si estás preocupado por el funcionamiento de tus sistemas de aire acondicionado o de proceso, o si has notado que el sistema no ha mejorado incluso después de un mantenimiento y reparaciones regulares, incluso un pequeño desbalanceo puede desempeñar un papel oculto para mantener su espacio incómodo o aumentar sus costos operativos. El proceso de TAB ayudará a identificar cualquier problema que pueda no ser evidente al solucionar un problema puramente mecánico.
Además, el reporte del TAB es una herramienta invaluable para garantizar que tu sistema se instale de acuerdo con las especificaciones de diseño adecuadas.
Si deseas garantizar el desempeño de tus sistemas de aire acondicionado nuestros servicios de Consultoría en Ingeniería, Energía y Sostenibilidad son tu mejor opción. ¡Contáctanos!
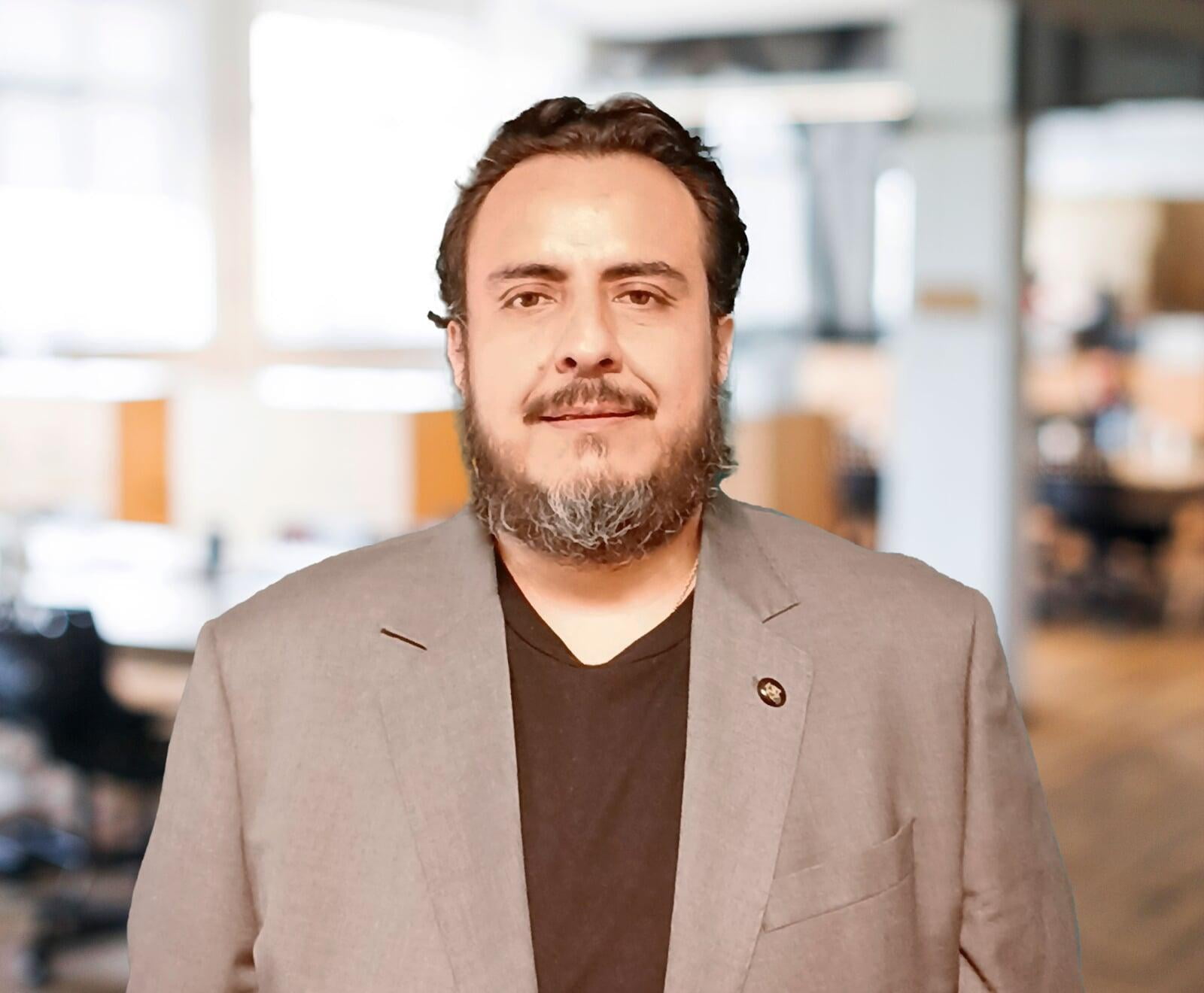
José Luis Arcos
Coordinador HVAC
Con más de 14 años de experiencia en sistemas de HVAC (Heating, Ventilation, Air Conditioning), ha desarrollado actividades en el área de diseño, instalación y TAB de sistemas de climatización en bancos, centros de telecomunicaciones, retail, hoteles, centros comerciales y edificios. En 2016 se unió a KINENERGY como especialista en comisionamiento en HVAC, donde se ha enfocado en el desarrollo de pruebas funcionales a sistemas de HVAC para certificación LEED hasta la realización de pruebas integrativas de Commissioning nivel 5.