Como se mencionó en la primera parte de este artículo, Six Sigma es una filosofía que se centra en aumentar la calidad y reducir los errores en cualquier tipo de proceso. Su meta es la mejora continua hasta alcanzar un nivel 6 de Sigma a través de la metodología “DMAIC” (Define, Measure, Analyze, Improve, Control).

Pero ¿cuáles son las razones para implementar Six Sigma dentro de mi empresa u organización?
- Permite tener controlados los procesos en todo momento, establecer variables medibles para analizar la operación de cada área de la empresa u organización, así como, definir cambios o nuevas estrategias para mejorar la eficiencia.
- Ayuda a eliminar errores durante los procesos.
- Contribuye a la creación de una identidad empresarial u organizacional que se basará en la búsqueda de la calidad total, así como de la excelencia.
- Favorece a incrementar la productividad y la rentabilidad de los productos o servicios, gracias a la mejora de los procesos y de la amortización de las inversiones.
- Involucra a todos los profesionales de la empresa y a todas sus áreas. La mejora de los procesos debe realizarse de forma conjunta para que la parte operativa funcione de forma homogénea y sin fisuras.
- Es aplicable a cualquier sector industrial y comercial.
Implementación de Six Sigma de manera práctica
Se sabía que existía una gran variabilidad en el ensamble de la carrocería de este auto, debido a que una vez que se encontraba ensamblado pasaba por el CMM (Cordinate Measuring Machine) en donde un brazo robótico se aproximaba a la carrocería en puntos específicos de medición y se obtenía el valor de las discrepancias en los 3 ejes de acuerdo con el ideal precargado en el robot (coordenadas base).
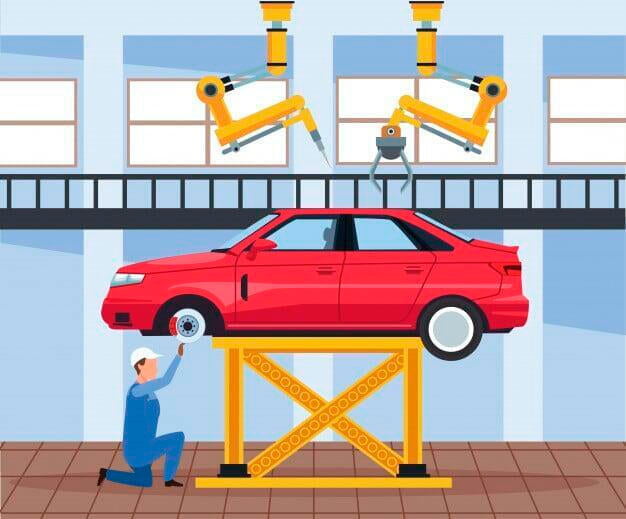
Este problema generaba una gran cantidad de retrabajos en líneas posteriores, pues existían discrepancias que dificultaban la instalación de los parabrisas, afectaba las holguras y “desenrases” de las puertas. Todo lo anterior iba en contra de un buen proceso “Lean” ya que existía una baja calidad, sin mencionar los retrabajos y el tiempo extra que era dedicado por especialistas en la “línea final”.
Tras la implementación del proceso DMAIC, se encontró que el punto de mejora se situaba en la línea de “welding” justo donde el robot punteador iniciaba el ciclo de ensamblado en la línea “Body”. En esta parte de proceso personal calificado de la planta tenía que colocar las subpartes de la carrocería en una prensa que lo sujetaría mientras el robot punteador realizaba la soldadura para unir dichas subpartes. Esta prensa tenía seis “clamps” que sujetaban las piezas para ser soldadas, y existía un orden de activación de dichos “clamps” con actuadores neumáticos, este procedimiento se llevaba a cabo por un obrero calificado.
Se hicieron numerosas pruebas cambiando el orden en que el los “clamps” sujetaban las piezas, se documentó cada prueba y se analizaron los resultados. Se determinó el orden más adecuado y se implementó una prueba piloto con la nueva secuencia hasta que se estableció como la solución ideal para reducir la variabilidad en ese proceso de subensamble.
Posterior a la implementación de estas mejoras se monitorearon las mediciones del ensamble en el CMM (Cordinate Measuring Machine), se realizaron mediciones y observaciones en la línea final y se percibió el cambio y la mejora se había obtenido con la implementación de la metodología.
La mejora involucró:
- Análisis de la data obtenida y el establecimiento de una nueva secuencia de “enclampado” (sujeción de la pieza en el ensamble).
- Implementación de un microcontrolador de serie Zelio Logic para automatizar el proceso mencionado.
- La programación del controlador.
- Monitoreo de los resultados de CMM y línea final durante 3 meses.
Conclusiones
Con una inversión de $150,000 MXN aproximadamente (incluidas horas hombre del personal calificado en el proyecto) la mejora que se logró obtener fue una reducción del 27% en la variabilidad de dicho proceso. Lo cual se puede ver traducido en una reducción de retrabajos y tiempo extra en la línea final, correspondiente económicamente a un ahorro aproximado de $ 70,000 MXN por mes.
Finalmente, se obtuvieron números bastante positivos en términos de ROI (Return On Investment), pues en menos de tres meses de mantener la mejora, aunado a una buena estrategia de mantenimiento, la utilización de TPM (Total Productive Maintenance) seguramente se podrá mantener por varios meses más e inclusive podría ser hasta por años un proceso eficiente en términos de variación y calidad.
Este fue un caso exitoso que requirió de una inversión mínima, sin embargo, no se debe perder de vista que su éxito fue gracias (casi en totalidad) al sistema de implementación de “Six Sigma” en la planta armadora, pues esto conlleva un sin número de acciones encaminadas a la profesionalización del personal de la planta.
Este caso nos muestra que la capacitación y actualización de nuestro personal, de nuestra gente y de los colaboradores de cada empresa y organización es de suma importancia, ya que ellos son el verdadero motor de éstas.
En KINENERGY podemos apoyar a tu empresa para implementar la metodología Six Sigma, y en dicho proceso, asesorar al personal para su adecuada aplicación. ¿Te interesa saber más? ¡CONTÁCTANOS!
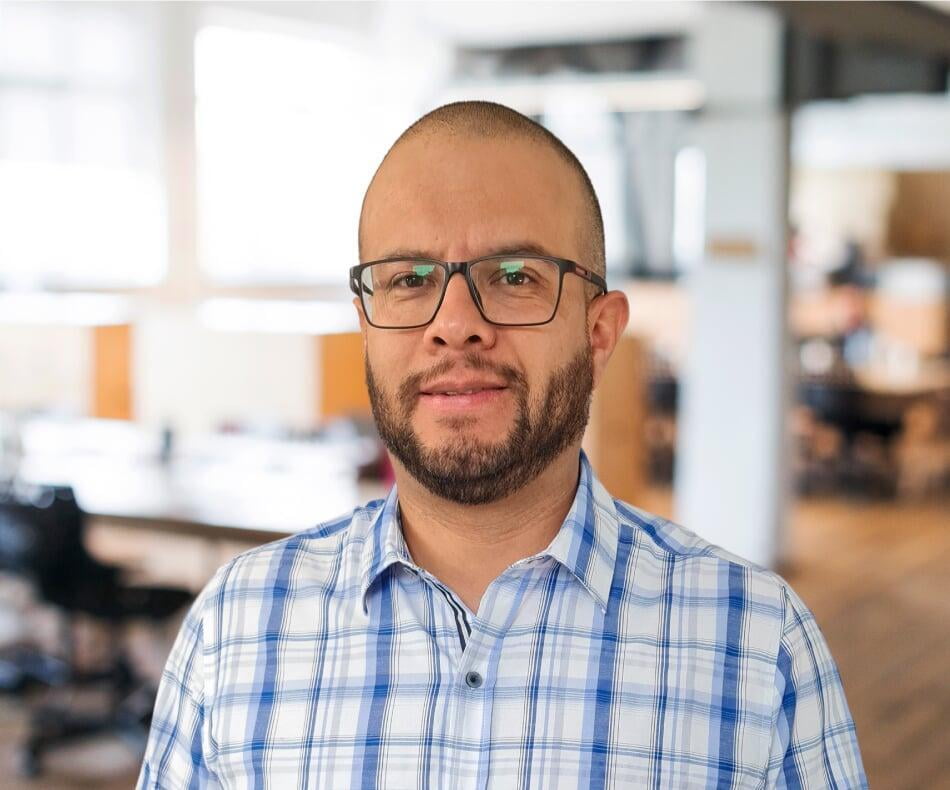
Saúl Santana
Manager de tecnologías
Saúl cuenta con 18 años de experiencia en ingeniería, ocupando cargos como superintendente de instalaciones, líder de gabinete y gerencia MEP, su área con mayor dominio es automatización, cuenta con especialidad en Lean Manufacturig (GB Six Sigma) y acreditación LEED AP O&M.