Como lo vimos en la primera parte de este artículo, enfrentar las fugas de gas refrigerante es crucial para la eficiencia y sostenibilidad de los sistemas de refrigeración industrial y comercial, pues estas fugas no solo comprometen el rendimiento operativo, sino que también generan impactos ambientales y financieros considerables.
En esta segunda parte, exploraremos en detalle la clasificación de las fugas, las legislaciones vigentes en México, los puntos de fuga más comunes y las mejores prácticas para la instalación de sistemas de refrigeración y aire acondicionado. Además, revisaremos las normas y estándares aplicables, ¡acompáñanos!
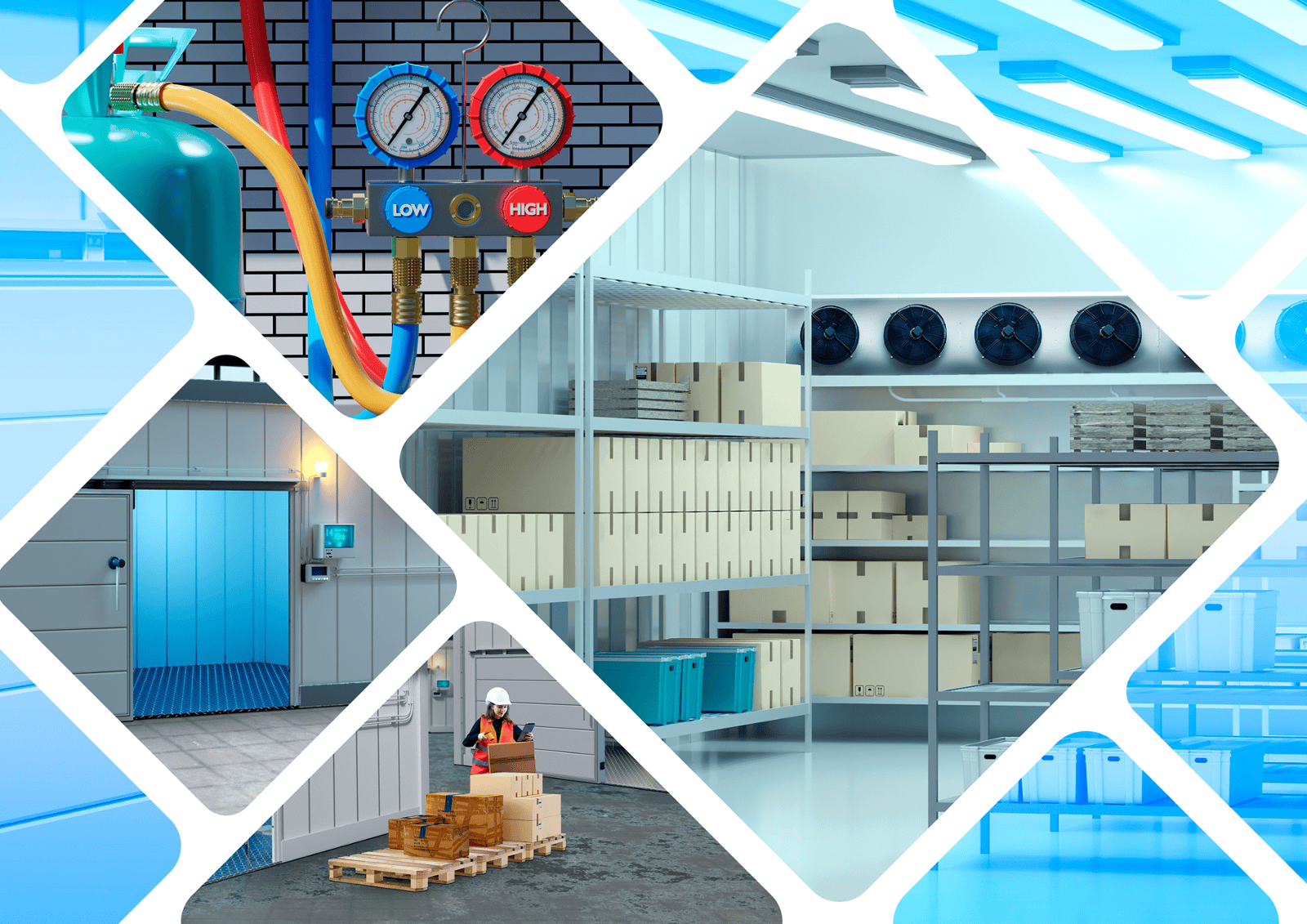
Clasificación de las fugas de gas refrigerante
Clasificación de las fugas de gas refrigerante
Las fugas de gas refrigerante se pueden clasificarse en:
- Emisiones difusas: fugaces y difíciles de localizar, generalmente causadas por roturas, accidentes inesperados o la degradación de la estanqueidad. Para manejarlas, es recomendable utilizar detectores portátiles y transmisores de ambiente para identificar la fuente de la fuga con mayor precisión.
- Degradación de la hermeticidad: la hermeticidad en un sistema de refrigeración puede verse afectada por cambios en la temperatura, presión y vibraciones.
- Roturas: las roturas suelen ser causadas por una instalación deficiente. Para prevenirlas, es crucial aplicar medidas correctivas durante la instalación y realizar mantenimiento regular y preventivo.
Legislación en México
Legislación en México
En México, la legislación sobre la gestión de sustancias peligrosas y la responsabilidad ambiental es estricta. buscando proteger el medio ambiente y los recursos naturales. A continuación, se detallan las principales leyes y artículos:
- Código Penal Federal.
Artículo 414: Establece penas para quienes manejen sustancias peligrosas sin las medidas de seguridad adecuadas. Las sanciones incluyen prisión de uno a nueve años y multas de entre 300 y 3,000 días de salario. También, se sanciona a quienes permitan acciones que causen daño a los recursos naturales o al medio ambiente.
- Ley Federal de Responsabilidad Ambiental.
Artículo 10: Este artículo establece la responsabilidad de cualquier persona física o moral que cause daño al medio ambiente, ya sea directa o indirectamente. La ley exige que el responsable repare los daños ocasionados, y en caso de que la reparación no sea posible, se debe realizar una compensación ambiental de acuerdo con lo establecido por la ley.
Artículo 24: Las personas morales (empresas, organizaciones) son responsables por los daños ambientales causados por sus representantes, administradores, gerentes, directores, empleados, o cualquier persona que tenga control funcional sobre las operaciones de la organización. La responsabilidad se atribuye si estas personas actúan de manera negligente, omisa, o en el ejercicio de sus funciones en nombre de la persona moral, o si consienten o autorizan acciones que resulten en daño ambiental.
Artículo 25: Este artículo aclara que los daños al medio ambiente pueden ser atribuidos a una persona física o moral que omitió tomar medidas para evitar el daño, siempre y cuando tuviera la obligación jurídica de hacerlo. El daño se considera resultado de una conducta omisiva si se determina que la persona tenía el deber de actuar, basado en una ley, contrato, su rol de garante, o acciones previas.
Puntos de fuga ¿qué son y cuáles son los más comunes?
Puntos de fuga ¿qué son y cuáles son los más comunes?
Como se mencionó anteriormente, las fugas en sistemas de refrigeración pueden llevar a pérdidas significativas de refrigerante, incrementando el consumo energético y los costos operativos. Los puntos de fuga más comunes en sistemas de refrigeración incluyen:
1. Componentes maniobrables:
- Válvulas de servicio: frecuentemente sujetas a desgaste o incorrecta instalación.
- Tapones: pueden ser una fuente de fugas si no están bien sellados.
2. Componentes roscables:
- Conexiones abocardadas (Flare): pueden fallar debido a una instalación inadecuada.
- Conexiones SAE: su diseño puede hacerlas propensas a fugas si no se aprietan adecuadamente.
- Válvulas de servicio (obuses): sus juntas o sellos pueden deteriorarse con el tiempo.
3. Componentes desmontables:
- Filtros: pueden desarrollar fugas en las juntas o conexiones.
- Bridas: pueden aflojarse o desgastarse, causando fugas.
4. Otros componentes:
- Condensadores: las fugas pueden ocurrir debido a corrosión o daño físico.
- Evaporadores: pueden tener fugas debido a fallos en los intercambiadores de calor.
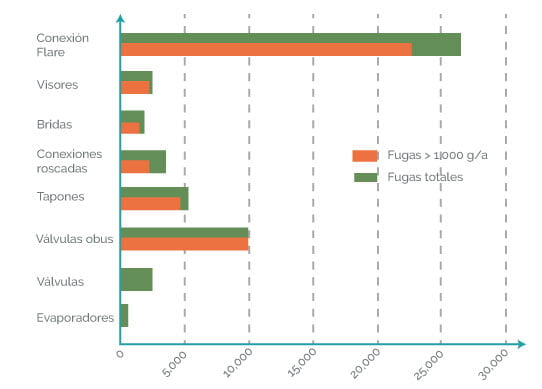
Buenas prácticas para la instalación de sistemas de refrigeración comercial y aire acondicionado
Buenas prácticas para la instalación de sistemas de refrigeración comercial y aire acondicionado
Según las directrices establecidas por la U.S. Environmental Protection Agency Stratospheric Protection Division en el documento “GreenChill Best Practices Guideline: Ensuring Leak-Tight Installations of Commercial Refrigeration Equipment”, es fundamental seguir varios procedimientos de verificación para garantizar la ausencia de fugas.
Y aunque estas recomendaciones se aplican principalmente a instalaciones de refrigeración comercial, como cámaras y vitrinas, sus principios también son relevantes para sistemas de aire acondicionado debido a la similitud en su operación.
El primer paso en la verificación de un sistema de refrigeración es realizar una inspección visual preliminar. Este proceso implica varias actividades clave como la revisión de tubos y uniones, el chequeo de soportes y conexiones y la inspección de uniones mecánicas.
Durante el proceso de soldadura con barridos de nitrógeno, es esencial mantener una presión de nitrógeno activa entre 1 y 5 psi. Este barrido con nitrógeno ayuda a prevenir la formación de óxido cúprico, que puede deteriorar las uniones soldadas y causar fugas, ya que las soldaduras sin nitrógeno pueden llevar a la oxidación del cobre, creando puntos débiles que podrían resultar en fugas.
Una vez completadas las inspecciones preliminares y las soldaduras, se debe proceder a la prueba de presurización:
- Aislamiento de los componentes: aislar los componentes que no sean adecuados para los niveles de presión establecidos. Esto es especialmente importante para condensadores y evaporadores, que a menudo ya vienen probados de fábrica en los sistemas de aire acondicionado; pero para sistemas de refrigeración comercial, hay que considerar que estos componentes pueden no estar cargados con refrigerante y requieran pruebas adicionales.
- Selección del gas trazador: utilizar nitrógeno seco como gas trazador y evitar el uso de refrigerantes durante la prueba de presurización.
- Apertura de válvulas: asegurar que todas las válvulas estén abiertas antes de comenzar la prueba.
- Ejecución de la prueba de presurización: cargar el sistema con nitrógeno seco regulado, y si es necesario, con el gas trazador adecuado, para elevar la presión del sistema a un mínimo de 300 psi. Verificar los puntos de acceso para confirmar la presurización.
Las derivaciones del sistema pueden ser probadas en segmentos para reducir el tiempo necesario. Sin embargo, para la prueba final, todas las válvulas deben estar abiertas. Si se detecta una fuga, debemos seguir estos pasos:
- Aislar la fuga del resto del sistema.
- Realizar las reparaciones necesarias.
- Volver a probar el área para confirmar que la fuga ha sido reparada.
- Re presurizar el área a un mínimo de 300 psi.
Normas y estándares
Normas y estándares
De acuerdo con el ASME B31.5, la prueba de presurización debe realizarse a una presión de 1.5 veces la presión de diseño o de operación del sistema y el BSEN 378, nos indica que la prueba de presurización debe llevarse a cabo con la siguiente fórmula:
Presión de prueba de estanqueidad = 1.0 × PS
Donde PS es la “Presión Máxima Permitida (PS)”, también conocida como la “Presión Máxima de Funcionamiento Permitida (MAWP)”, está diseñado para operar de manera segura y se indica en la placa de identificación del recipiente (esta presión puede ser igual o mayor que la presión de diseño del sistema).
Antes de continuar debemos asegurarnos de que todas las válvulas que se cerraron para aislar la fuga estén abiertas nuevamente después de la reparación.
Evaluación previa del vacío del sistema
Evaluación previa del vacío del sistema
Para asegurar un vacío adecuado y eliminar nitrógeno, aire y humedad, que pueden causar bloqueos por hielo en la válvula de expansión y acumulación de cera y ácido en el aceite, se deben seguir ciertos pasos preliminares.
Primero, debemos asegurarnos de que el sistema esté completamente despresurizado, para así poder conectar la bomba de vacío en al menos dos puntos del sistema de refrigeración (la bomba debe tener una capacidad mínima de 8 CFM) y se debe cambiar el aceite lubricante según las recomendaciones del fabricante. Además de utilizar un medidor de micrones adecuado que sea capaz de medir hasta 300 micrones.
Procedimiento de evacuación por triple vacío
Procedimiento de evacuación por triple vacío
Es importante recordar que los requisitos de vacío pueden variar según las especificaciones del cliente y/o normativas.
Comenzamos realizando un vacío en el sistema hasta alcanzar al menos 1000 micrones (+/- 50 micrones) y luego debemos cerrar las válvulas del encabezado de vacío. Si el sistema no puede mantener el vacío y vuelve a la presión atmosférica, indicar una fuga y realizar las pruebas y reparaciones necesarias siguiendo el procedimiento con gas trazador previamente descrito.
Si el vacío de 1000 micrones se mantiene durante 30 minutos, romper el vacío con nitrógeno seco hasta alcanzar una presión de 2 psig, posteriormente se debe realizar un segundo vacío hasta un mínimo de 500 micrones. Si el vacío de 500 micrones se mantiene durante al menos 30 minutos, rompa el vacío con nitrógeno seco o con el refrigerante que se utilizará en el sistema, alcanzando una presión de 2 psig.
Finalmente debemos se tiene que proceder con un tercer vacío hasta alcanzar un mínimo de 300 micrones y posteriormente cerrar las válvulas del sistema de refrigeración. Dejar que el sistema repose durante al menos 24 horas. Si el vacío de 300 micrones se mantiene durante 24 horas con una variación máxima de 100 micrones, el sistema está listo para ser cargado con refrigerante, por último, romper el vacío con el refrigerante que se utilizará en el sistema y llenar el sistema hasta alcanzar la presión estática correcta en ambos lados (baja y alta presión).
Procedimientos adicionales para equipos de precisión
Procedimientos adicionales para equipos de precisión
Para algunos equipos de precisión, se pueden requerir procedimientos adicionales específicos. Estos incluyen presurizar el sistema a 200 o 150 psi, según corresponda, y demostrar que el sistema mantiene la presión durante 24 horas.
Además, se debe documentar el proceso fotografiando las conexiones del vacuómetro e indicando la presión atmosférica. Los registros de vacío deben incluir mediciones a 5000 micrones, 2000 micrones, 1000 micrones, 500 micrones, y finalmente a 250 micrones antes de apagar la bomba. También, se debe demostrar que el vacío se mantiene durante un mínimo de 4 horas antes de romper el vacío con refrigerante.
En KINENERGY, entendemos que abordar todos estos aspectos de manera integral es clave para prevenir problemas y garantizar el funcionamiento seguro de los sistemas.
Si tienes alguna duda o necesitas asesoramiento, nuestro equipo de expertos está preparado para ayudarte a implementar estas prácticas con éxito, ¡déjanos tus datos!
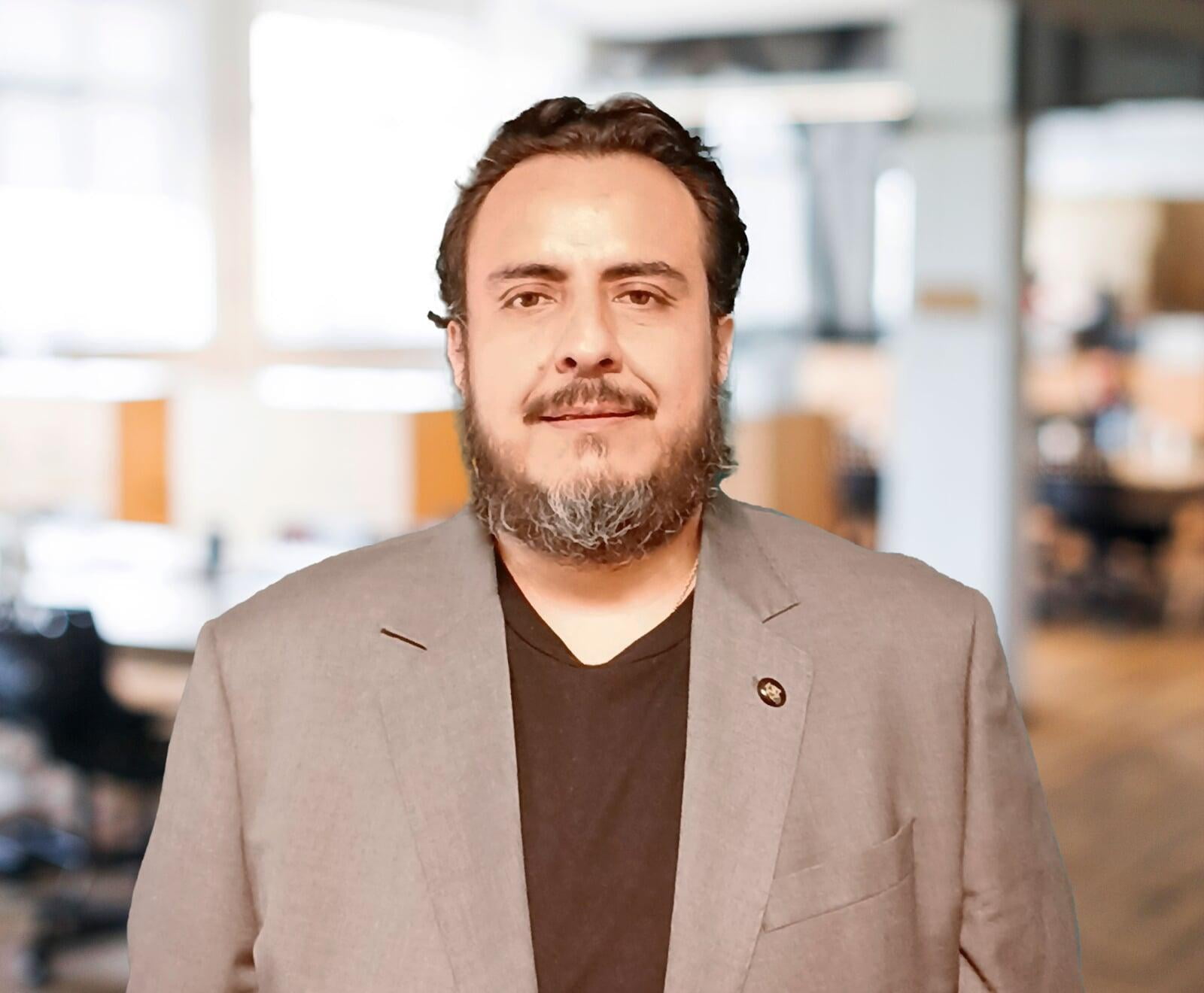
José Luis Arcos
Coordinador HVAC
Coordinador HVAC
Cuenta con más de 14 años de experiencia en sistemas de HVAC (Heating, Ventilation, Air Conditioning), ha desarrollado actividades en el área de diseño, instalación y TAB (Testing, Adjusting and Balance) de sistemas de climatización en bancos, centros de telecomunicaciones, retail, hoteles, centros comerciales y edificios.
En 2016 se unió a KINENERGY como especialista en comisionamiento en HVAC, donde se ha enfocado en el desarrollo de pruebas funcionales a sistemas de HVAC para certificación LEED hasta la realización de pruebas integrativas de commissioning nivel 5, de igual manera ha participado en diversos proyectos realizando pruebas de Cx, TAB, pruebas a envolvente y de integrity room, en México, Centroamérica y Sudamérica.
Cuenta con más de 14 años de experiencia en sistemas de HVAC (Heating, Ventilation, Air Conditioning), ha desarrollado actividades en el área de diseño, instalación y TAB (Testing, Adjusting and Balance) de sistemas de climatización en bancos, centros de telecomunicaciones, retail, hoteles, centros comerciales y edificios.
En 2016 se unió a KINENERGY como especialista en comisionamiento en HVAC, donde se ha enfocado en el desarrollo de pruebas funcionales a sistemas de HVAC para certificación LEED hasta la realización de pruebas integrativas de commissioning nivel 5, de igual manera ha participado en diversos proyectos realizando pruebas de Cx, TAB, pruebas a envolvente y de integrity room, en México, Centroamérica y Sudamérica.
Referencias:
ASHRAE 34-2022 y ASHRAE 15-2022 para normativas de seguridad en refrigerantes.
Acuerdo de Kigali, 2016: reducción gradual de HFC.
Refrigerant Loss, System Efficiency and Reliability – A Global Perspective; GEA Refrigeration UK Ltd for Institute Of Refrigeration (IOR). ©Institute of Refrigeration Annual Conference 2013.